Ball Mill Efficiency Rpm
.jpg)
Ball Mill Critical Speed 911Metallurgist
2015年6月20日 — A Ball Mill Critical Speed (actually ball, rod, AG or SAG) is the speed at which the centrifugal forces equal gravitational forces at the mill shell’s inside surface and no balls will fall from its position onto the shell2021年3月12日 — efficient grinding systems available for the cement and mineral industry, including vertical roller mills (VRM), highpressure grinding units (HPGR) or simple roller BALL MILLS Ball mill optimisation Holzinger Consulting2017年10月26日 — The following are factors that have been investigated and applied in conventional ball milling in order to maximize grinding efficiency: a) Mill Geometry and Speed – Bond (1954) observed grinding efficiency Factors Affecting Ball Mill Grinding Efficiency2020年7月2日 — A comprehensive investigation was conducted to delineate the effect of ball size distribution, mill speed, and their interactions on power draw, charge motion, and (PDF) Effects of Ball Size Distribution and Mill Speed and
.jpg)
Effects of Mill Speed and Air Classifier Speed on
2021年6月29日 — The research focuses on the mill speed as well as air classifier speed effect on the two compartment Cement ball mill performance in terms of Blaine, Sulphur trioxide contents, mill power,2021年2月19日 — The optimum process parameters setting concluded that balls to powder weight ratio are 20:1, the optimum ball mill working capacity is 2 L while the optimum Comparative Study on Improving the Ball Mill Process 2024年9月18日 — This paper will describe CSE and how it is measured in practice Next, a guide for improving CSE through manipulation of design and operating variables in the guide to maximising ball mill circuit classification system 2020年12月17日 — Ball size is one of the key factors of ballmill efficiency [11, 12], and may have a significant financial impact [13] The population balance model (PBM) has been widely used in ball mills [14] This model Kinetics of DryBatch Grinding in a Laboratory
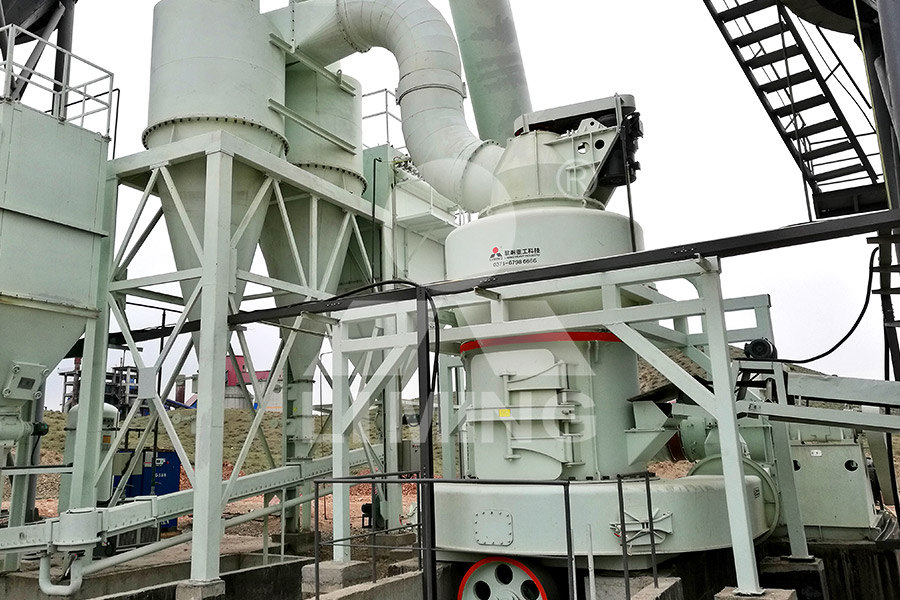
Modeling and Analysis of HighEnergy Ball Milling Through Attritors
2017年7月5日 — The simulation reveals that the ball milling velocity, ball volume fraction inside the canister, ball size, and impeller shaft design are all important parameters for 释文:磨矿的目的是使矿石磨到选别要求的粒度,达不到规定的粒级称“磨不细”,而磨到选别难于回收的粒级则称“过粉碎”,磨机技术效率可从产品粒度上反映磨矿目的实现的程度。 磨机技术效率 百度百科2024年8月8日 — Unlock the secrets to ball mill efficiency with our comprehensive guide on choosing the right grinding media Learn how material composition, size, shape, hardness, and cost impact your milling Ball Mill Success: A StepbyStep Guide to The characteristic tumbling motion of these mills has given them the name ‘tumbling mills’, which include the ball mill, tube mill and rod mill Ball mills are horizontal rotating cylindrical or conical steel chambers, approximately one third to half full of steel, alloy steel or iron balls, like that shown in Fig 410 A–C , or flint stonesBall Mill an overview ScienceDirect Topics
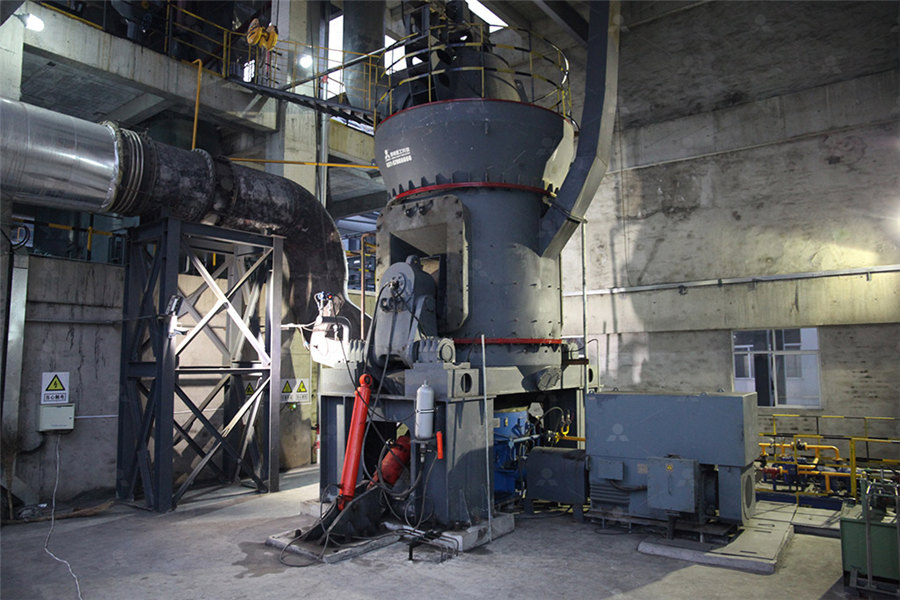
Comparative Study on Improving the Ball Mill Process
2021年2月19日 — The optimum process parameters setting concluded that balls to powder weight ratio are 20:1, the optimum ball mill working capacity is 2 L while the optimum speed of the ball mill is 105 rpm Using SEM characterization, the improved particles of silica sand presented a spherical shape with a cluster2021年6月29日 — Nowadays, ball mills are widely used in cement plants to grind clinker and gypsum to produce cement The research focuses on the mill speed as well as air classifier speed effect on the two Effects of Mill Speed and Air Classifier Speed on 2021年2月26日 — Milling is among the most energyconsuming technological stages of copper ore processing It is performed in mills, which are machines of high rotational masses The start of a mill filled to capacity requires appropriate solutions that mitigate the overloading One method for increasing the energy efficiency of ball mills is to optimize Energy Efficiency Analysis of Copper Ore Ball Mill Drive This means that during one rotation of the sun wheel, the grinding jar rotates twice in the opposite direction This speed ratio is very common for Planetary Ball Mills in general Planetary ball mills with higher energy input and a speed ratio of 1:25 or even 1:3 are mainly used for mechanochemical applicationsPlanetary Ball Mills RETSCH fine grinding of materials
.jpg)
Design and Analysis of Ball Mill For Paint Industries IJSRD
2014年10月10日 — (and have variable speed settings) for more efficient processing C Industrial Ball Mills Industrial ball mills are much larger than the other types of ball mills They vary in size from approximately the size of minute (rpm) for a ball mill is directly related to the ball mill radius, these two factors are grouped together to studyTo study the operation of a Ball mill and to calculate the efficiency of a Ball mill for grinding a material of known work index (Wi) To study the effect of RPM on the power consumption of Ball mill To calculate the critical speed (ηc) of a Ball mill Introduction: Generally the Ball mills are known as the secondary size reduction equipmentBall mill BALL MILL EXPERIMENT MANUAL Title of Experiment: Ball Enhanced Performance and Efficiency Recent advancements in laboratory ball mill technology have been steadfast in the pursuit of improving performance and efficiency Manufacturers are constantly pioneering innovative solutions to refine the milling process, enabling researchers to achieve superior results in less timeLaboratory Ball Mill Exploring the Latest Innovations in Ball Mill Introduction There are three main stages to mineral processing in the mining industryThese are: Comminution (crushing and grinding); Beneficiation (separation and concentration); Smelting and refining; Ball mills are employed in the comminution stage as grinding machines (size reduction)The purpose of grinders in the mining industry is to Ball Mill (Ball Mills Explained) saVRee saVRee
]@S0{UDKK%G24F3JGHC.jpg)
Mechanistic modeling and simulation of a wet planetary ball mill
2023年11月1日 — A summary of the results from the DEM simulations is presented in Table 7, which shows that the collision frequency in the simulations of tests with 63 mm balls and 50% mill filling was six times higher than that with balls measuring 10 mm and 35% mill filling, both in a mill rotating at a frequency of 200 rpm2024年9月24日 — The average ball mill can achieve upwards of 90% grinding efficiency; however, this varies depending on a number of factors including type of material being processed, size of balls used, RPM setting, etcGrinding efficiency of ball mill calculating equation2024年4月28日 — the other mills, as previously mentioned ball mills have a very low efficiency in terms of utilizing the energy generated towards particle size reduction The diameter of the balls used in ball mills play a significant role in the improvement and optimization of the efficiency of the mill [4] The optimum rotation speed of a mill, which is The Effect of Ball Size Diameter on Milling Performance2022年9月1日 — It means the mill at 70 rpm consumes more power but causes less particle breakage Through analysis, the additional energy (around 92%) consumed at 70 rpm is wasted by the ballball collisions and the rest is more small and ineffective damping energy contacts Larger mill size is more efficient for ball milling process because particles are A DEM based scaleup model for tumbling ball mills
.jpg)
Ball Mill Performance Efficiency Formulas
Ball Mill Performance Efficiency Formulas IF YOU WORK IN A CEMENT PLANT AND YOU NEED COURSES AND MANUALS LIKE THIS MANUAL AND BOOKS AND EXCEL SHEETS AND NOTES I SPENT 23 YEARS COLLECTING THEM YOU SHOULD CLICK HERE TO DOWNLOAD THEM NOW rpm: Deff: Mill effective diameter, mts: Pn:With 37 years of industry experience, JXSC has built a reputation as a leading ball mill manufacturer among ball mill manufacturers Since 1985, With over 200 successful mining projects in more than 40 countries, JXSC has been providing premium services, from RD and production to installation and free operation training Applying steel balls as grinding Ball Mills Manufacturer JXSC2012年6月1日 — efficiency of the ball mill and the economic assessment of the process control R e f e r e n c e s 1 A j a a l, T, R W S m i t h, W T Y e n The Development and Characterization of a Ball (PDF) Grinding in Ball Mills: Modeling and Process ControlRetsch visualises the features and strengths of each ball bill model in a diagram to help finding the right model for a specific application In the example shown it is easy to see that the Planetary Ball Mill PM 300 offers advantages in terms of power, final fineness and maximum jar volume compared to the Mixer Mill MM 500 controlBall Mills Suitable for every application Retsch

(PDF) Grinding Media in Ball MillsA Review ResearchGate
2023年4月23日 — One of the most used tumbling mills is the ball mill This paper reviews different types of grinding media that have been developed and improved over the years and their properties2018年2月1日 — In another study to investigate ball size distribution on ball mill efficiency by Hlabangana et al [50] using the attainable region technique on a silica ore by dry milling, a threeball mix of Effect of ball and feed particle size distribution on the milling 2024年4月30日 — where R = radius of ball mill; r = radius of ball For R = 1000 mm and r = 50 mm, n c = 307 rpm But the mill is operated at a speed of 15 rpm Therefore, the mill is operated at 100 x 15/307 = 4886 % of critical speed If 100 mm dia balls are replaced by 50 mm dia balls, and the other conditions are remaining the same, Speed of ball mill Ball Mill Operating Speed MSubbu AcademyAnalysis of the efficiency of the grinding process in closed circuit ball mills Valery I Telichenko1, Rashid R Sharapov1*, Svetlana YLozovaya2 and Vladimir ISkel1 1Moscow State University of Civil Engineering, Moscow, Russia 2Belgorod State Technological University named after VG Shukhov, Belgorod, Russia Abstract Ball mills for fine Analysis of the efficiency of the process in closed circuit
.jpg)
Grinding Efficiency Between Bead Mill and Ball
2023年9月5日 — In the experiment, the sand mill used zirconia balls with a diameter of 15mm (15 kg), while the ball mill and vibration mill used a mixture of zirconia balls with diameters of 20mm, 15mm, and Click to request a ball mill quote online or call 6303503012 to speak with an expert at Paul O Abbe® to help you determine which design and size ball mill would be best for your process See our Size Reduction OptionsVariables in Ball Mill Operation Paul O Abbe2020年7月2日 — A comprehensive investigation was conducted to delineate the effect of ball size distribution, mill speed, and their interactions on power draw, charge motion, and balls segregation in a (PDF) Effects of Ball Size Distribution and Mill Speed and 2023年12月29日 — COMPARISON OF GRINDING EFFICIENCY BETWEEN BALL MILLS AND VERTICAL ROLLER MILLS IN COARSE GRINDING Yakup Umucu 1, Vedat Deniz 2,Osman Mart 1 Abdi Kemal Y!ce 1, Mehmet Fahri Sara" 3 1 S leyman COMPARISON OF GRINDING EFFICIENCY BETWEEN
.jpg)
Size reduction performance evaluation of HPGR/ball mill and
2023年1月1日 — X 1, X 2 and X 3 are the mill speed (rpm), grinding time (min), and ball size (mm), respectively The ANOVA analysis for the P 80 and the energy consumption model is given in Table 4 The pvalues lesser than 005 signify the rejection of the null hypothesis at a 95% confidence level, indicating that a particular term in the model significantly 2015年6月19日 — The basic parameters used in ball mill design (power calculations), rod mill or any tumbling mill sizing are; material to be ground, characteristics, Bond Work Index, bulk density, specific density, desired mill tonnage capacity DTPH, operating % solids or pulp density, feed size as F80 and maximum ‘chunk size’, product size as P80 and maximum Ball Mill Design/Power Calculation 911Metallurgist2024年9月15日 — The HP is influenced by the mill diameter, length, and rotation speed A higher HP mill is capable of processing more material per hour but may also require a more powerful motor and a larger foundation 3 Rotation Speed: The rotation speed of the ball mill, typically measured in revolutions per minute (RPM), affects the grinding efficiencyUnderstanding ball mill specifications for optimal 2022年3月22日 — The size of grinding media is the primary factor that affects the overall milling efficiency of a ball mill (eg power consumption and particle size breakage) This article tackles the lack of a design tool that could help choose the ball loading Critical speed 105 rpm Operational speed 84 rpm Ball charge Diameter of balls 195, 38, 50 mm Effect of grinding media on the milling efficiency of a
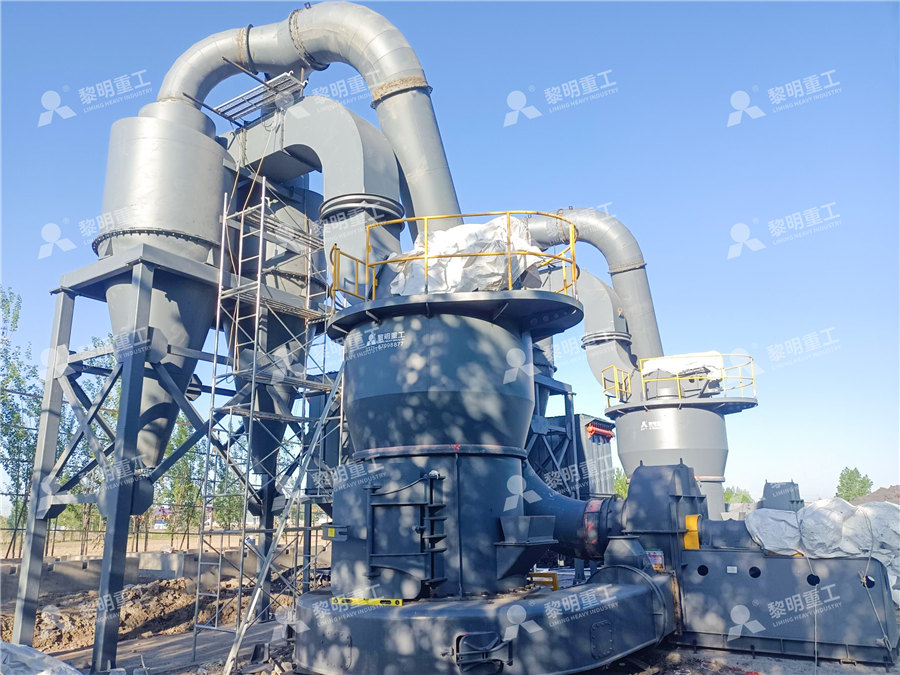
Planetary Ball Milling and Tailoring of the Optoelectronic
2023年10月31日 — Downscaling of tin monoselenide (SnSe) samples to the nanometer regime (~80–20 nm) without affecting the structure, homogeneity, and optoelectronic properties was carried out by highenergy planetary ball milling (BM) The milling rate was varied from 200 rpm to 800 rpm by adopting a dry and wetgrinding topdown approach 2017年7月3日 — The voids (or interstitial space) within a rod load are approximately half those in a ball mill grinding load Rods in place weigh approximately 400 pounds per cu ft and balls in place approximately 300 pounds per cu ft This permits maximum grinding efficiency at the maximum rate possible before an overload occurs In addition, this Ball Mills vs Rod Mills 911Metallurgist2021年3月27日 — Effect of ball and feed particle size distribution on the milling efficiency of a ball mill: An attainable region approach N Hlabangana a, G Danha b, *, E Muzenda b a Department of Chemical Engineering, National University of Science and Technology, P O Box AC 939, Ascot Bulawayo, Zimbabwe b Department of Chemical, Materials and Effect of ball and feed particle size distribution on the 2023年9月22日 — chemical industries are subjected to grinding in ball mills [1–3] The specic energy consumption for these materials typically ranges from 5 to 50 kWh/ton Thus, the ball mills consume an enormous amount of energy The energy eciency of the ball mill being as low as 1% or less [2], there is considerable incentive to improve the energy eciencySelected Advances in Modelling of Size Reduction in Ball
.jpg)
Finally got a ball mill, Tips? Tools and Tooling APC Forum
2021年6月14日 — I use this media in my ball mill works great 1/2Inch Hardened Lead Ball Milling Media — Skylighter, Inc but mine runs at around 75 RPM The only way you can use both jars is with ceramic media, the cheapest (and least efficient) choice If you do use the single component or double component method, stainless steel is your ideal media 2009年6月1日 — At product sizes finer than 80% passing 75 μm, the efficiency of ball mill grinding rapidly decreasesThe practical limit to ball mill product fineness is considered to be 40–45 μm (Gao and Weller, 1994)Although ball mills can still be found in the regrind circuits in a number of mineral processing plants, their energy consumption is high, and size Comparison of energy efficiency between ball mills and stirred mills 2023年2月20日 — Ball mills and Raymond mills The RPM (rotations per minute) of a ball mill depends on the diameter of the mill and the desired particle size and grinding efficiency However, as a general rule of What should be the RPM of a ball mill with a 45inch 2024年6月3日 — Biochariron based material has been recognized as an important soil and underground water remediation material, which successfully achieves by adsorption, reduction, and mediating advanced oxidationResearch progress on synthesis mechanism and performance
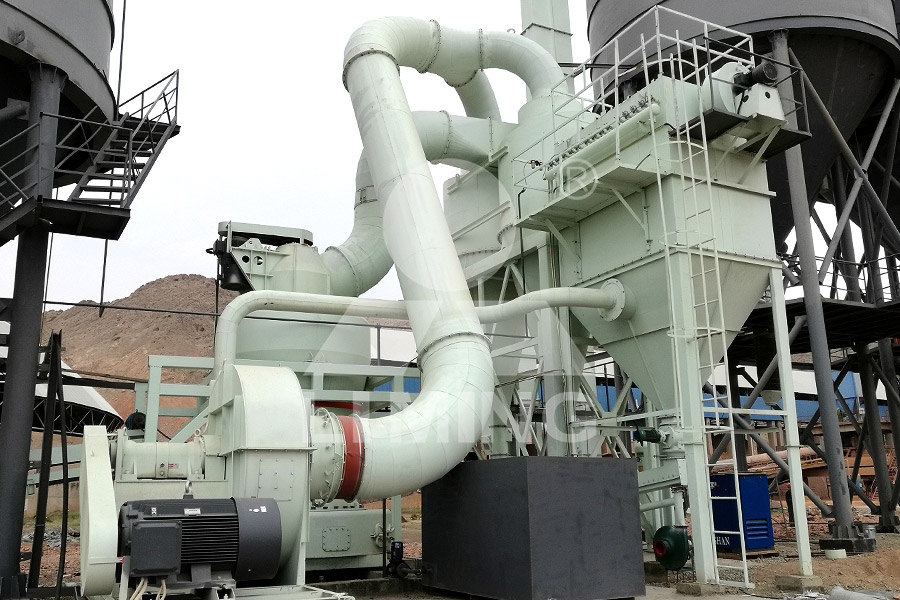
Evolution of grinding energy and particle size during dry ball
2020年10月1日 — The sample is stirred at 2000 rpm during 5 min in order to eliminate potential bubbles The specific selection function effect on clinker grinding efficiency in a dry batch ball mill Int J Miner Process, 87 (3–4) (2008), pp 141145, 101016/jminpro200802003The mill used for this comparison is a 44meter diameter by 136 meter long ball mill with a 5000 HP drive motor It is designed for approximately 90 ston per hour This type twocompartment mill is a state oftheart shell supported cement finish mill The torque and time requirements of the mill with the ballBALL MILL DRIVE MOTOR CHOICES Artec Machine2024年8月8日 — Unlock the secrets to ball mill efficiency with our comprehensive guide on choosing the right grinding media Learn how material composition, size, shape, hardness, and cost impact your milling Ball Mill Success: A StepbyStep Guide to The characteristic tumbling motion of these mills has given them the name ‘tumbling mills’, which include the ball mill, tube mill and rod mill Ball mills are horizontal rotating cylindrical or conical steel chambers, approximately one third to half full of steel, alloy steel or iron balls, like that shown in Fig 410 A–C , or flint stonesBall Mill an overview ScienceDirect Topics
CFB石灰石脱硫剂制备96.jpg)
Comparative Study on Improving the Ball Mill Process
2021年2月19日 — The optimum process parameters setting concluded that balls to powder weight ratio are 20:1, the optimum ball mill working capacity is 2 L while the optimum speed of the ball mill is 105 rpm Using SEM characterization, the improved particles of silica sand presented a spherical shape with a cluster2021年6月29日 — Nowadays, ball mills are widely used in cement plants to grind clinker and gypsum to produce cement The research focuses on the mill speed as well as air classifier speed effect on the two Effects of Mill Speed and Air Classifier Speed on 2021年2月26日 — Milling is among the most energyconsuming technological stages of copper ore processing It is performed in mills, which are machines of high rotational masses The start of a mill filled to capacity requires appropriate solutions that mitigate the overloading One method for increasing the energy efficiency of ball mills is to optimize Energy Efficiency Analysis of Copper Ore Ball Mill Drive This means that during one rotation of the sun wheel, the grinding jar rotates twice in the opposite direction This speed ratio is very common for Planetary Ball Mills in general Planetary ball mills with higher energy input and a speed ratio of 1:25 or even 1:3 are mainly used for mechanochemical applicationsPlanetary Ball Mills RETSCH fine grinding of materials
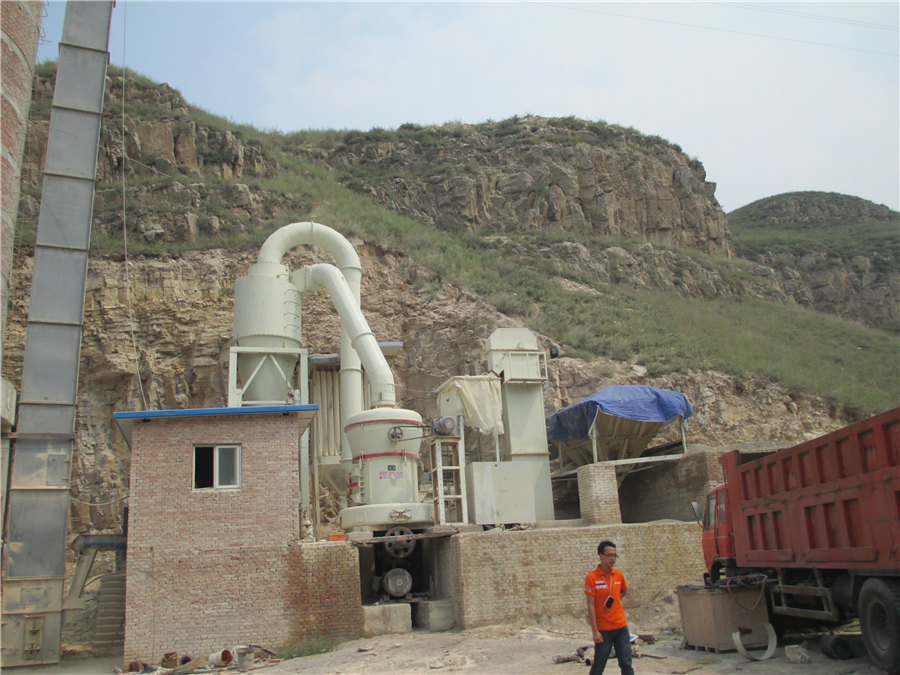
Design and Analysis of Ball Mill For Paint Industries IJSRD
2014年10月10日 — (and have variable speed settings) for more efficient processing C Industrial Ball Mills Industrial ball mills are much larger than the other types of ball mills They vary in size from approximately the size of minute (rpm) for a ball mill is directly related to the ball mill radius, these two factors are grouped together to studyTo study the operation of a Ball mill and to calculate the efficiency of a Ball mill for grinding a material of known work index (Wi) To study the effect of RPM on the power consumption of Ball mill To calculate the critical speed (ηc) of a Ball mill Introduction: Generally the Ball mills are known as the secondary size reduction equipmentBall mill BALL MILL EXPERIMENT MANUAL Title of Experiment: Ball Enhanced Performance and Efficiency Recent advancements in laboratory ball mill technology have been steadfast in the pursuit of improving performance and efficiency Manufacturers are constantly pioneering innovative solutions to refine the milling process, enabling researchers to achieve superior results in less timeLaboratory Ball Mill Exploring the Latest Innovations in Ball Mill Introduction There are three main stages to mineral processing in the mining industryThese are: Comminution (crushing and grinding); Beneficiation (separation and concentration); Smelting and refining; Ball mills are employed in the comminution stage as grinding machines (size reduction)The purpose of grinders in the mining industry is to Ball Mill (Ball Mills Explained) saVRee saVRee